Fermented Bioplastics: Turning Microbes into a Solution for Plastic Pollution
- Arun Luthra
- Apr 15
- 22 min read

Fermented Bioplastics: Turning Microbes into a Solution for Plastic Pollution
Plastic is everywhere in our modern lives – from packaging and consumer goods to medical devices – but its convenience comes at a steep environmental cost. Traditional petroleum-based plastics take hundreds of years to break down and are polluting our land and oceans at an alarming rate. In response, a new generation of bioplastics (plastics made from renewable biological sources) is emerging as a sustainable alternative. This blog will introduce different types of bioplastics – especially those made via fermentation – and explore how they can help tackle plastic pollution. We’ll look at the impact of plastic on the environment, compare bioplastics to conventional plastics, highlight fermented-based biopolymers like PLA and PHA, and share real-world case studies of companies leading the way.
The Environmental Toll of Traditional Plastics
Since the 1950s, humans have produced over 9 billion tons of plastic, yet only about 9% of it has ever been recycled renouvo.net. The rest accumulates in landfills or leaks into the environment, with an estimated 165 million tons of plastic debris already in the oceansrenouvo.net. Every year, roughly 9 million more tons of plastic waste enter the oceansrenouvo.net. This flood of plastic pollution has become one of Earth’s most pressing environmental challenges.
In the ocean, plastics persist for centuries, breaking apart into tiny microplastics rather than truly decomposing. These particles have permeated every level of the marine food web, from plankton to whales. For example, blue whales may ingest around 10million microplastic pieces per day as they filter feed rts.com. Wildlife often mistake plastic for food or become entangled in it. It’s estimated that over 1 million marine animals (mostly seabirds) die each year due to plastic pollution, along with over 100,000 marine mammals rts.com. Scientists have even found microplastics in human organs and blood, indicating how far this contamination has spread through the food chain.
Plastic pollution doesn’t only threaten ocean life; it also contributes to climate change and environmental degradation on land. Plastics are made from fossil fuels – extracting and producing them releases significant greenhouse gases and pollutants oceancare.org. And when discarded plastic is incinerated, it releases carbon dioxide, further worsening climate impacts oceancare.org. In summary, our “disposable” plastic habit has created a global pollution crisis, driving the search for better materials that can reduce harm to wildlife and ecosystems.
What Are Bioplastics?
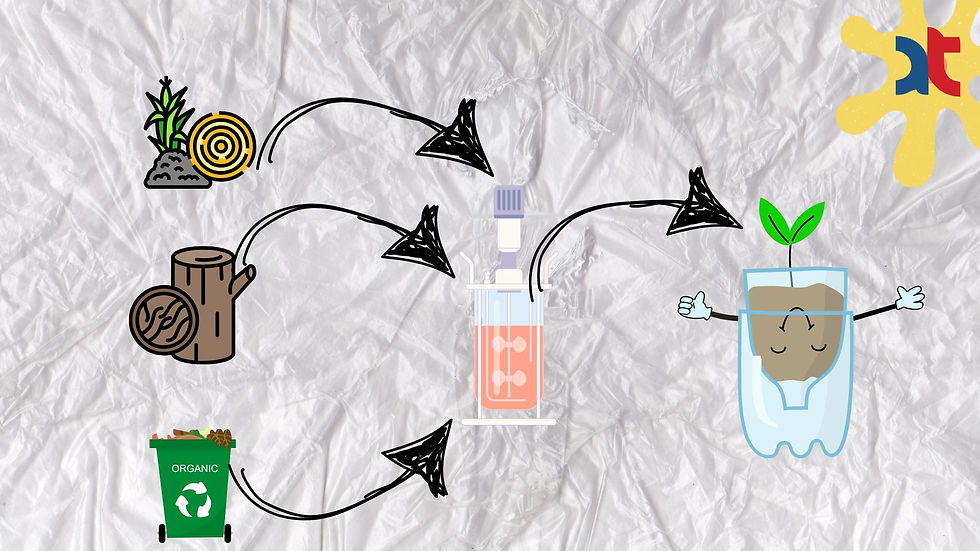
It’s important to clarify that “bioplastic” does not automatically mean “biodegradable.” Some bioplastics are bio-based (made from plants) but behave like traditional plastic in the environment, while others are specifically engineered to biodegrade (be broken down by microbes) under certain conditions, greenbusinessbenchmark.comgreenbusinessbenchmark.com. In this post, we focus on bioplastics that are both bio-based and biodegradable, since these offer the greatest environmental benefits. By replacing fossil resources with renewable ones and ensuring the material can safely return to nature at end-of-life, such bioplastics aim to solve the issues of traditional plastic’s lifecycle.
Common Types of Bioplastics
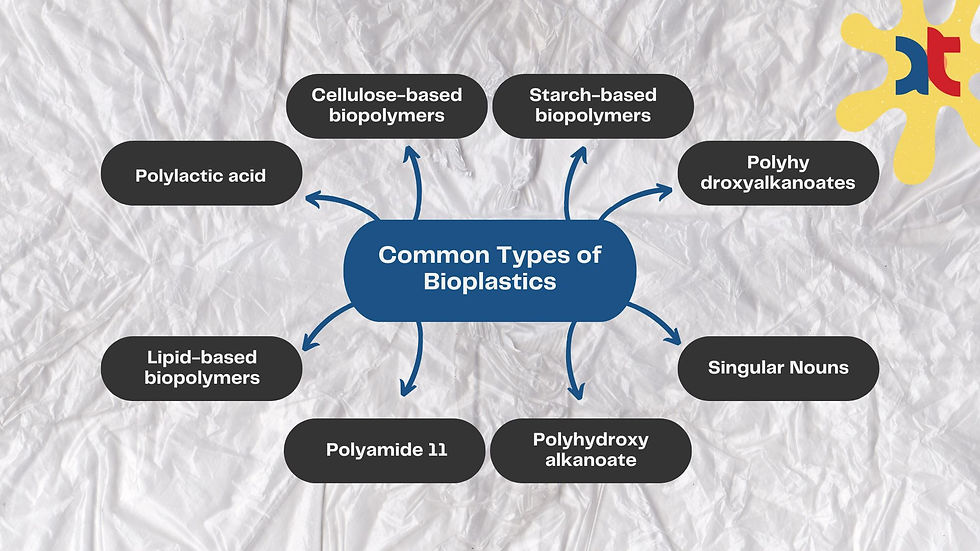
There are several main families of bioplastics on the market today, each with different properties and production methods. Below is an overview of some key types, including PLA, PHA, and starch-based bioplastics – with a special emphasis on those produced via fermentation.
Polylactic Acid (PLA): PLA is one of the leading bioplastics in use today. It’s a biodegradable thermoplastic polyester made from renewable plant sugars – typically derived from corn starch or sugarcane. Manufacturers ferment plant sugars to produce lactic acid, which is then chemically polymerized into PLApackagingeurope.com. The result is a plastic that looks and behaves much like conventional petroleum plastics: PLA is transparent, strong, and moldable, which makes it popular for packaging (food containers, bottles, wrappers), disposable cutlery, and even 3D printing filament. Unlike PET or polyethylene, PLA is compostable – under the high-heat, microbial-rich conditions of industrial composting facilities, PLA can break down into water, CO₂, and organic matter. This means when PLA products (like compostable cups or utensils) are disposed properly in compost, they can biodegrade in a matter of months. However, PLA does not readily biodegrade in normal ambient environments like soil or seawater. In fact, PLA needs the controlled conditions of an industrial composter (heat around 60°C and moisture) to decompose efficientlycbsnews.com. If a PLA item ends up in a landfill or the ocean, it might persist for years (though likely still shorter than conventional plastic). Overall, PLA’s bio-based origin and compostability give it a smaller carbon footprint and waste impact than traditional plastics, as long as it is handled in the correct end-of-life stream.
Polyhydroxyalkanoates (PHA): PHA represents a family of truly biodegradable plastics that are garnering a lot of excitement. PHAs are unique because they are produced directly by microorganisms through fermentation. Certain bacteria (such as Ralstonia eutropha or Pseudomonas species) can synthesize PHA granules inside their cells as energy storage compounds when fed plant sugars or oils packagingeurope.comrenouvo.net. To make PHA plastic, manufacturers cultivate these microbes in fermenters, feed them renewable carbon sources (like sugar, vegetable oil, or even methane gas), then harvest and refine the polymer that the bacteria accumulate. The resulting PHA polymer can be molded into various products just like conventional plastic resin. What makes PHA especially attractive is its impressive biodegradability across many environments. PHA will naturally break down in soil, compost, marine water, and freshwater, as microbes in those environments digest it businessinsider.comrenouvo.net. In other words, a PHA straw or bag that accidentally blows into the ocean could biodegrade within months – a stark contrast to petroleum plastic that might drift for centuries. Moreover, PHA tends to leave no toxic residue; it biodegrades into biomass, carbon dioxide, and water, with no microplastic fragments left behindrenouvo.net. PHAs are also biocompatible, meaning they can safely interact with living tissues – this has led to medical uses like dissolvable sutures and implants. Currently, PHAs are being used in items like compostable foodservice ware (e.g., utensils, straws), packaging films, coatings, and even textiles. One challenge is that PHA production is still relatively expensive and small-scale, so PHAs make up only a tiny fraction of the plastic market. But their unique advantages – fully renewable, and truly biodegradable in nature – make them a key focus in the quest for sustainable plastics.
Starch-Based Plastics: Starch-based bioplastics are a simpler type made by processing natural starch (from corn, potatoes, tapioca, etc.) into plastic-like materials. Starch by itself can be made thermoplastic by adding plasticizers (like glycerol) and heat, transforming it into a material that can be formed into films or foam-like packaging. Often, starch-based plastics are blended with other biodegradable polymers (such as PLA or biodegradable polyesters like PBAT) to improve their material properties greenbusinessbenchmark.com. These blends are commonly used for products like compostable shopping bags, organic waste bin liners, food packaging foam peanuts, and disposable tableware greenbusinessbenchmark.com. Starch-based bioplastics have the benefit of using an abundant, cheap, renewable feedstock and they generally biodegrade relatively easily, since starch is readily consumed by microbes. For example, a thin starch-based grocery bag can biodegrade in a home compost or soil within a few months under the right conditions. However, pure starch plastics can be brittle or sensitive to water (think of how starch dissolves), so manufacturers often mix them with other materials to make them stronger or more water-resistant. The end products are usually compostable as well. One well-known success of starch bioplastics is in compostable plastic bags – some countries and cities have adopted compostable bags made from starch blends to replace traditional polyethylene bags, thereby reducing litter and facilitating organic waste collection. While not as high-tech as PLA or PHA, starch-based plastics play a significant role in the bioplastics industry by replacing single-use items that don’t need high durability.
(Other bioplastics include materials like cellulose-based plastics, or bio-derived versions of conventional plastics (e.g. bio-PE made from sugarcane ethanol). However, the examples above cover the most widely used categories, especially those that are both bio-based and designed to biodegrade.)
Fermented-Based Bioplastics: Harnessing Microbes for Sustainability
One of the most exciting fronts in sustainable materials is the use of fermentation – the same type of process that produces beer or yogurt – to manufacture plastics. In fermented-based bioplastics, we essentially let microorganisms serve as tiny factories that convert renewable raw materials into polymer building blocks or even into polymers themselves. Both PLA and PHA introduced above rely on fermentation in their production: PLA uses fermentation to get lactic acid, and PHA is made by microbial fermentation directly into a polymer. Leveraging fermentation offers some unique advantages in making plastics more sustainable:
Fermentation-based production of bioplastics relies on specialized bioreactors where microbes convert sugars or other renewable feedstocks into valuable polymers. These processes can run year-round and are not tied to seasonal crop harvests, making supply more consistent. By feeding microbes with waste biomass, agricultural byproducts, or even greenhouse gases, fermentation can produce plastics with a much lower environmental footprint than petrochemicals.
Use of Diverse, Renewable Feedstocks: Fermentation allows manufacturers to use non-petroleum inputs ranging from plant sugars and starches to biowaste, CO₂, or methane as the raw material packagingeurope.com. For instance, sugars from corn or sugarcane can be fed to microbes, but so can organic waste streams like food waste or gases from landfills. This flexibility means fermented bioplastics can avoid competing directly with food crops and can even upcycle waste materials into new plastics. Some fermentation processes have achieved carbon-negative status by consuming methane (a potent greenhouse gas) and locking its carbon into plastic. In short, fermentation opens the door to using cheap, abundant resources – even pollutants – to make useful materials.
Lower Fossil Energy Use & Emissions: Because the carbon in fermented bioplastics comes from plants or waste (which originally absorbed CO₂ from the atmosphere), the overall carbon footprint can be much smaller than conventional plastic. If the process uses renewable energy and especially if it utilizes waste carbon, it can significantly cut net greenhouse gas emissions. One analysis found that producing PLA from municipal waste could lead to a net 73 kg CO₂ reduction per ton of plastic produced, compared to conventional production. Likewise, making PHA was shown to reduce fossil energy use by 95% and greenhouse gas emissions by over 200% (meaning it can be net carbon-negative) in certain casespackagingeurope.com. In essence, fermented bioplastics have the potential for a much cleaner lifecycle, emitting far less CO₂ and pollutants than making petroplastic (which involves drilling oil, refining, cracking, etc., all of which are carbon-intensiveoceancare.org).
Biodegradability by Design: The fermentation route often yields polymers that microorganisms recognize as food. After all, microbes created these polymers, so many microbes can also degrade them. PHA is a prime example – it was “born” inside a bacterium, and when a PHA product enters a compost or marine environment, other bacteria and fungi can readily metabolize it. This is a stark advantage over synthetic plastics that most microbes cannot digest. By tailoring the fermentation conditions and microbial strains, scientists can even tweak polymer composition to adjust how quickly it biodegrades. This built-in biodegradability means fermented bioplastics are well aligned with natural cycles – ideally, after use, they can be broken down by the same ecosystem that produced their ingredients in the first place.
Not Weather-Dependent: Traditional bio-based materials (like certain crops or plant fibers) might depend on agricultural cycles and large land areas. Fermentation, however, is an industrial process that runs in tanks, so it’s not constrained by weather or seasonspackagingeurope.com. Fermenters can operate continuously and be located anywhere (even next to a waste treatment plant to use its waste as input). This decoupling from agriculture means more consistent output and potentially avoiding the use of prime farmland solely for plastic production. It also allows for modular, decentralized production – small fermentation facilities could be set up near various biomass sources.
Product Customization: Modern biotechnology allows us to program microbes (through selection or genetic engineering) to produce specific molecules. This gives a degree of customizability in fermented bioplastics. For example, by changing the microbe or feedstock, companies can produce different types of PHA (there are many variants like PHB, PHBV, etc., with different properties – one might be stiffer, another more flexible). Fermentation processes can also produce monomers with certain chirality or functionality (the packaging industry has even explored fermenting precursors for bio-based polyesters with tailored properties). In short, fermentation can yield a wide range of polymer chemistries tuned for various applications, something that is harder to achieve with directly extracting polymers from plants.
Of course, fermentation is a sophisticated endeavor – it requires investment in biotech R&D, fermentation infrastructure, and careful control of conditions to be efficient. But rapid advances in synthetic biology, enzyme engineering, and process technology are making it ever more viable. As we’ll see next, several companies have already scaled up fermented bioplastics and are beginning to deliver products that consumers use in everyday life.
Case Studies: Bioplastics in Action
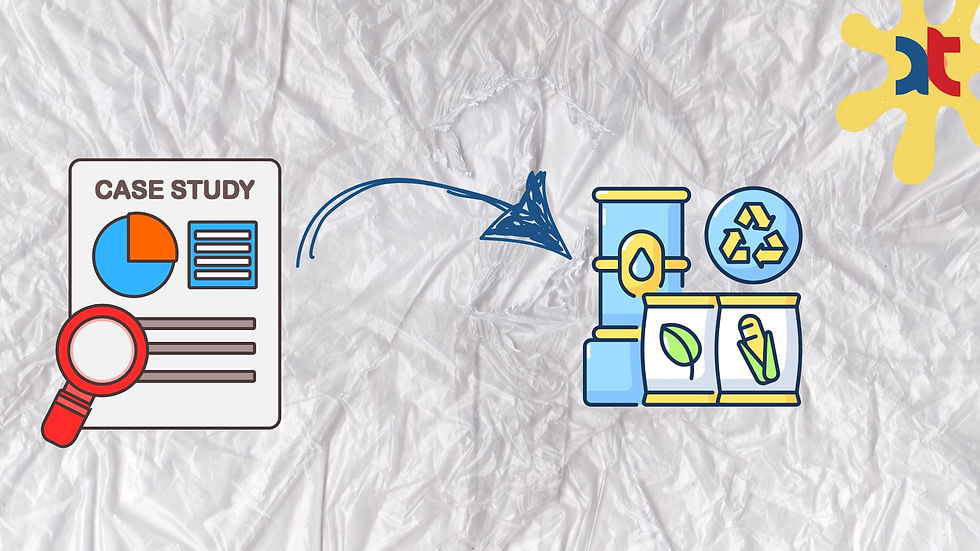
Real-world examples of fermented bioplastics are popping up around the globe, indicating that these materials are moving beyond the lab. Here are a few case studies and initiatives that demonstrate how companies and communities are leveraging PLA, PHA, and other bioplastics to replace conventional plastics:
NatureWorks (PLA Producer) – From Corn to Compostable Cups: NatureWorks, based in the USA, is the world’s largest PLA manufacturer. This company (a joint venture of agribusiness giant Cargill and PTT Global Chemical) uses corn sugar to feed bacteria that produce lactic acid, which is then converted to Ingeo™ PLA plastic. NatureWorks’ plant in Nebraska can produce 150,000 metric tons of PLA per year cbsnews.com, and a new $600 million facility under construction in Thailand will boost capacity by 50%cbsnews.com. PLA from NatureWorks is used worldwide in products like compostable cold drink cups, yogurt containers, and even the lining inside certain paper cups. For instance, some Starbucks stores have trialed disposable cups lined with NatureWorks PLA instead of a polyethylene liner cbsnews.com – this makes the cups fully compostable in industrial facilities. By turning crops into packaging that can then break down into soil nutrients, NatureWorks is helping to close the loop between agriculture and packaging waste. (NatureWorks has also recognized PLA’s limitations in biodegrading outside compost facilities, and has partnered with a PHA producer to create new blends that biodegrade more easily cbsnews.comcbsnews.com.)
Danimer Scientific (PHA Producer) – Biodegradable Straws and Bottles: Danimer Scientific is a U.S.-based company at the forefront of PHA bioplastics. At its Kentucky facility, Danimer ferments canola oil with special bacteria to produce a PHA polymer branded as Nodax™ PHA cbsnews.com. The PHA comes out as resin pellets that can be used in standard plastic molding equipment to make products. Danimer’s PHA gained fame for being used in the world’s first fully biodegradable plastic drinking straw in 2018 businessinsider.com. Major brands have since adopted Danimer’s PHA for single-use items: for example, Starbucks and Dunkin’ Donuts have introduced PHA-based straws and stirrers in certain locations, which perform like plastic but will biodegrade after disposal cbsnews.comcbsnews.com. Danimer also collaborated with Bacardi, the spirits company, to develop a PHA liquor bottle that can biodegrade in 18 months after use businessinsider.com. Starting in 2023, Bacardi plans to roll out these PHA bottles (alongside paper bottles for some brands) to replace 80 million traditional plastic bottles used across their product lines businessinsider.combusinessinsider.com. The PHA bottle will completely break down without leaving microplastic fragments, even in environments like seawater and soil businessinsider.com. Danimer’s CEO notes that tests show their PHA items can biodegrade in about 6 months in marine conditions and around 2 years in soil cbsnews.com – a dramatic improvement over the centuries that conventional plastic persists. By scaling up PHA production (Danimer’s expanded plant has made it one of the world’s largest PHA producers cbsnews.com), they are demonstrating that fermentation-derived plastics can work in mainstream applications from food service to packaging, with far less ecological impact.
Mango Materials – Turning Methane Emissions into PHA: One innovative startup, Mango Materials based in California, is taking a novel carbon source for fermentation: methane, a greenhouse gas typically flared or vented from landfills and wastewater plants. Mango Materials uses methane-eating microbes in fermentation tanks to produce PHA biopolymer, essentially converting waste biogas into biodegradable plasticwaste360.comwaste360.com. They have been piloting their technology at a wastewater treatment facility in Silicon Valley and have scaled up to a 5,000-liter fermenter in Vacaville, CA waste360.com. By capturing methane that would otherwise contribute to global warming and using it to create PHA, their process is not only renewable but potentially carbon-negative (since it locks carbon into a usable form) waste360.com. Mango Materials has targeted high-value products first – their PHA was initially used to make a biodegradable soap dish for a cosmetics company and stylish sunglasses for fashion brand Stella McCartney waste360.com. They even contributed a PHA component for a carbon-negative shoe in partnership with Allbirds (a sustainable footwear company) waste360.com. These niche products can bear the higher cost of early production. Now, Mango Materials is working on PHA microfibers that could replace polyester in fabrics, as well as film and injection-molded applications like compostable packaging and toys waste360.com. Their vision is to deploy networks of decentralized fermenters at sites with methane supply, each turning a local pollution source into biodegradable plastic resinwaste360.comwaste360.com. This model exemplifies circular economy thinking: waste gas in, useful plastic out, then back to nature. Mango’s success, backed by partnerships with industry (e.g. Black & Veatch for engineering and BioMADE for fundingwaste360.com), shows how biotech innovation can tackle pollution on multiple fronts.
Community Initiatives and Policies: It’s not only companies, governments and communities are also driving adoption of bioplastics. For example, Italy was one of the first countries to ban conventional single-use plastic shopping bags nationwide and mandate compostable bags (often made from starch-based bioplastic) for groceries and produce. This policy rapidly increased the use of biodegradable starch blend bags, which consumers can reuse to collect food scraps and then compost. Similarly, the European Union’s directive to reduce single-use plastics has led food service providers to seek compostable alternatives for items like plates, cutlery, and straws – boosting demand for PLA and PHA products. In some cities, event organizers and cafeterias are switching to bioplastic utensils and cups to simplify waste management (all compostable waste can go in one bin instead of trying to separate recyclables). However, it’s worth noting that successful outcomes depend on having composting facilities or collection programs to actually process the biodegradable items. Still, these initiatives are important case studies showing real-world use of bioplastics at scale. They not only test the performance of these materials in everyday settings but also help educate the public about separating compostables from trash.
These case studies illustrate that fermented and bio-based plastics are no longer just experimental concepts – they’re being used in everything from coffee shops to fashion to major consumer goods. Each success builds knowledge on how these materials behave in practice (both in use and after disposal), helping improve future designs.
Bioplastics vs. Traditional Plastics: How Do They Compare?
With several types of bioplastics now available, it’s important to understand how they stack up against conventional plastics across key factors like biodegradability, lifecycle environmental impact, and cost. While no single material is perfect for all needs, bioplastics offer significant advantages in many of these categories, though there are also challenges to consider.

Biodegradability and End-of-Life
Traditional plastics (such as polyethylene, polypropylene, PET) are not biodegradable – they are extremely resistant to natural breakdown and can persist for centuries, fragmenting into microplastics but never fully reverting to organic moleculesgreenbusinessbenchmark.comgreenbusinessbenchmark.com. This means that every piece of standard plastic has to be either recycled (which happens to only ~9% of it greenbusinessbenchmark.com), incinerated, or landfilled; if littered, it becomes long-term pollution. In contrast, many bioplastics are designed to biodegrade under the right conditions. Compostable bioplastics like PLA, PHA, and starch blends can be broken down by microbes into benign natural substances. For example, certified compostable PLA cups or utensils will turn into CO₂, water, and compost within a few months in an industrial compost facility. PHA goes a step further – it will biodegrade in environments like soil, home compost, or seawater, given a bit more time businessinsider.comrenouvo.net. This means if PHA or starch-based items escape into nature, they are far less likely to accumulate and cause harm years down the line. However, it’s crucial to note that biodegradability is condition-dependent: even bioplastics require suitable microbes, temperature, and moisture to break down efficientlygreenbusinessbenchmark.comgreenbusinessbenchmark.com. PLA will remain intact in a cool ocean or a landfill for a long time because those environments are not conducive to PLA’s composting process cbsnews.com. PHA will biodegrade in marine water, but more slowly in cold oceans than in warm compost piles cbsnews.com. Thus, while bioplastics have a clear advantage of potential biodegradability, they are not a license to litter – proper disposal (e.g. sending to compost or anaerobic digestion when available) is still important to realize this benefit. The big upside is that if managed correctly, bioplastics can be part of a biological cycle (use, then biodegrade back to nature) instead of building up as permanent waste. They also tend to produce no harmful microplastics or toxic residues upon degradation renouvo.net, unlike petroplastics, which can leach additives as they slowly break apart renouvo.net.
Environmental Lifecycle Impact
From a lifecycle perspective, bioplastics generally have a smaller environmental footprint than traditional plastics, particularly in terms of carbon emissions and fossil resource depletion. Conventional plastics start with crude oil or natural gas; extracting and transporting those fossil fuels can cause habitat damage (e.g., oil spills) and require energy. Then the petrochemicals are polymerized in processes that emit significant CO₂. And at end-of-life, if plastics are incinerated, they release the carbon as CO₂; if landfilled, they can persist indefinitely. Bioplastics, by contrast, begin with renewable carbon that was recently pulled from the atmosphere by plants. Growing feedstocks like corn or sugarcane does use land, water, and fertilizers, but these plants also absorb CO₂ during growth, offsetting some emissions. Studies have found that PLA production can result in 25–75% lower greenhouse gas emissions than production of conventional plastics like PET (depending on assumptions)packagingeurope.com. PHA production can dramatically cut petroleum use and even result in net negative emissions when waste-based feedstocks are used packagingeurope.com. Additionally, making bioplastics avoids the toxins associated with oil refining and certain plastic additives; bioplastics are generally free of bisphenol-A (BPA) and phthalates, for example, which can be found in some conventional plasticsrenouvo.netrenouvo.net. At end-of-life, if bioplastics are composted, the carbon in them simply returns to the atmosphere or soil without adding new fossil carbon – essentially closing the carbon loop. And if some fraction of bioplastic ends up in the ocean or environment, it has a chance to biodegrade and not persist as long-term pollution, mitigating the harm compared to an equivalent piece of polyethylene. However, it’s not all automatically green: the lifecycle impact of a bioplastic can vary based on how its feedstock is grown (fertilizer and land use impacts), the energy used in production, and how it is disposed of. If a PLA item is improperly landfilled and not captured for compost, its environmental benefit is partly lost (though even landfilled PLA at least keeps its carbon sequestered and doesn’t emit methane unless conditions allow partial breakdown). Overall, when produced and managed optimally, bioplastics offer a significant reduction in environmental impact – they cut reliance on finite fossil fuels and can greatly reduce the plastic pollution and microplastic load on the planet.
Cost and Market Considerations
One reason bioplastics still comprise only about 1% of total plastics production cbsnews.comcbsnews.com is cost. Currently, bioplastics are generally more expensive to produce than high-volume petroplastics. The raw materials (like sugar or starch) and the fermentation/bioprocessing steps add cost compared to pumping oil (which benefits from a huge, optimized infrastructure). Estimates put many bioplastics at about 20–30% higher cost than conventional plastics on a per kilogram basis planetpristine.com. In 2023, for instance, PLA resin sold for around $2.3 per kg in North America businessanalytiq.com, whereas commodity polypropylene might be around $1.5 per kg. PHA is even newer and produced at a smaller scale, so its price can range from $4–$7 per kg or more in the current market planetpristine.com. These prices will come down as companies scale up production – and indeed, investment in bioplastic manufacturing is rapidly growing (over $500 million was invested in the first quarter of 2022 alone) cbsnews.com. Economies of scale and technological improvements are expected to make bioplastics cost-competitive with traditional plastics within the next decade planetpristine.complanetpristine.com. It’s worth noting that cost comparisons also shift if environmental externalities are considered – the long-term pollution and carbon emissions of conventional plastic impose costs on society that aren’t reflected in its price. Some governments are starting to incentivize alternatives or restrict certain single-use plastics, which effectively boosts the market for bioplastics. From a user perspective, the higher cost of bioplastics today often means they are used in premium or niche applications (e.g, eco-conscious brands, or areas with regulatory pressure). But as production capacity and demand increase, we’re seeing costs gradually decline and bioplastics entering more mainstream uses. Market research projects the bioplastics market to roughly triple from $10.5 billion in 2021 to $29 billion by 2028, cbsnews.comcbsnews.com. In summary, while traditional plastics still have an economic edge due to established supply chains and scale, the gap is closing. In the long run, the financial cost of bioplastics is expected to come down, while the environmental cost of sticking with conventional plastics is untenable. Many experts believe that as we factor in sustainability, bioplastics will prove not just better for the planet, but a smart economic choice too.
Fermented Bioplastics and the Path to a Circular Economy
A circular economy is a vision of an economic system where materials are kept in use for as long as possible and waste is designed out – resources cycle back into new products or the environment safely, rather than accumulating as pollution. Fermentation-based bioplastics have a key role to play in moving us toward that circular future by aligning plastic production and disposal with natural cycles.
PHA bioplastic resin pellets (shown above in hand) are an example of a circular material: they originate from renewable plant oils via microbial fermentation, and after their useful life, they can biodegrade into natural substances that feed back into the ecosystem. Such materials illustrate how we can re-imagine plastics as part of a sustainable cycle instead of a one-way stream to waste.
Closing the Loop with Renewable Carbon: Traditional plastics take carbon from deep underground (fossil fuels) and disperse it into the environment as waste and CO₂. Fermented bioplastics instead use renewable carbon from recent plant growth or recycled resources. A crop like corn or sugarcane absorbs CO₂ as it grows; when that plant is used to create PLA or PHA, the carbon is temporarily stored in a plastic item, and when that item biodegrades, the carbon returns to the atmosphere or soil to be reused by new plants. This is a short carbon cycle that, if managed properly, doesn’t increase net CO₂ in the atmosphere. In cases like PHA from methane, the carbon was a waste product that is now diverted into a useful loop (methane → PHA → CO₂ after biodegradation), preventing it from simply being emitted. Thus, bioplastics integrate with the natural carbon cycle instead of disrupting it.
Biological Recycling (Composting): Bioplastics that are compostable provide a form of “biological recycling.” Instead of sending used packaging to a landfill or incinerator, we can send it to an industrial compost facility or an anaerobic digester. In compost, materials like PLA, PHA, and starch plastic will break down alongside food scraps and yard waste, turning into nutrient-rich compost. This compost can then be used to enrich soil for agriculture, closing the loop by helping grow more plants. In an anaerobic digestion system (an oxygen-free process), biodegradable materials can be converted into biogas (methane) and a soil amendment – the biogas can be captured for energy, and the digested material can fertilize fields. Either way, fermented bioplastics ensure that the end-of-life of products isn’t the end at all, but rather the beginning of a new cycle. This circular approach contrasts sharply with the linear “take-make-dispose” model of traditional plastics.
Reducing Persistent Pollution: A circular economy also means future generations aren’t burdened with our waste. Because fermented bioplastics biodegrade fully into natural components, they don’t leave behind microplastics or toxic remnants that accumulate over time. For instance, a PHA bag that finds its way into the ocean will eventually be consumed by microbes and disappear, rather than adding to the Great Pacific Garbage Patch. By replacing items that would have been single-use plastics (like packaging, cutlery, etc.) with items that safely biodegrade, we gradually reduce the persistent plastic load in the environment. Over time, widespread adoption of such materials could significantly lower the amount of plastic pollution harming wildlife and clogging ecosystems. In a sense, fermented bioplastics enable a scenario where even if a product becomes “waste,” it can be a useful input to nature or industry rather than a pollutant.
Synergy with Recycling Systems: While composting is a form of recycling, some bioplastics can also be recycled conventionally or chemically to further keep materials in use. PLA, for example, can be collected and hydrolyzed back into lactic acid to make new PLA (this is not common yet, but pilot programs exist). PHA, being biodegradable, is a bit trickier to recycle mechanically (since it can start breaking down if stored wet), but researchers are exploring ways to bio-recycle PHA by feeding PHA waste to PHA-producing bacteria to make new polymermdpi.com. The ideal future might see a mix of recycling and composting such that we extract maximum value from materials and then return them to nature at the end. Fermentation processes themselves could be part of this circularity – imagine using bacteria to digest used bioplastic and ferment it back into raw monomers or new bioplastic, closing the loop even tighter.
Supporting Sustainability Goals: Many companies and governments have set sustainability and climate goals (for example, carbon neutrality by 2050, or zero plastic waste in nature by 2030). Fermented bioplastics directly contribute to these goals. They cut carbon emissions (helping with climate targets), use renewable or even waste inputs (reducing dependence on finite resources), and address the plastic waste issue by being truly biodegradable. In terms of the UN Sustainable Development Goals (SDGs), bioplastics touch on responsible consumption and production, climate action, life below water (less ocean pollution), and industry innovation. By adopting materials like PLA and PHA, companies can reduce the footprint of their products and packaging and demonstrate a commitment to a circular economy. For consumers, using a product made from fermented bioplastic carries the benefit that, after use, you can compost it or know that it will not linger as trash for generations. This transforms the consumer experience into a more sustainable one.
Finally, it’s worth acknowledging that building a circular economy is a collective effort – it involves designing products for end-of-life, developing infrastructure (like composting facilities), and educating consumers on proper disposal. Bioplastics are not a silver bullet for all environmental issues, but they are a powerful tool in our toolbox. When the chemistry of our materials aligns with Earth’s biology, we create systems that are regenerative by design.
Conclusion: Brewing a Sustainable Future
From the perspective of a few decades ago, the idea of brewing plastics in fermentation tanks or making bottles that microbes can eat would have sounded like science fiction. Yet today, fermented bioplastics like PLA and PHA are real and growing solutions to the plastic pollution problem. They demonstrate that we can enjoy the benefits of plastic – versatility, durability, convenience – without condemning the planet to centuries of pollution. By using renewable resources and cooperating with natural processes (via microbial fermentation and biodegradation), we are essentially bringing plastic full circle back into the web of life.
The fight against plastic pollution will require many strategies: reducing unnecessary single-use plastics, improving recycling systems, and cleaning up existing waste. Bioplastics address the problem at the source by reinventing what “plastic” can be. A cup made from fermented corn or a textile made from fermented methane is more than a novelty – it’s a statement that we can shape technology to work with nature rather than against it. Every compostable bag or PHA straw is a small victory for oceans and landscapes free of everlasting litter.
For educators and sustainability professionals, fermented bioplastics provide a tangible example of the circular economy in action, and a compelling story to share: microbes and humans working together to solve an environmental challenge. For the general public, these materials offer an accessible way to be part of the solution – for instance, by choosing compostable products when available and supporting brands that invest in sustainable packaging.
In the coming years, as research advances and production scales up, we can expect fermented bioplastics to become more common and cost-effective. Imagine supermarkets stocked with packaging that you can toss in your green compost bin, or electronics made with bio-based casings that can be efficiently recycled or biodegraded at end-of-life. Achieving that vision will take continued innovation and smart policy, but the momentum is building.
In conclusion, fermented-based bioplastics exemplify the notion of “innovation inspired by nature.” By learning from and leveraging biological processes, we are creating plastics that not only meet our needs but also respect the boundaries of our planet. It’s an exciting and hopeful development – one that suggests that perhaps the plastics of the future will leave no trace but nutrients and new possibilities for growth.
References:
Plastic pollution in the ocean and its impacts – statistics and factsrenouvo.netrts.com
Packaging Europe – Fermentation chemicals: A green revolution in bioplastics?packagingeurope.compackagingeurope.com
Renouvo – What is bioplastic? Types of bioplastics: PLA and PHArenouvo.netrenouvo.net
CBS News – Bioplastics made from natural materials (Danimer, NatureWorks case study)cbsnews.comcbsnews.com
Business Insider – Bacardi’s biodegradable bottle (PHA)businessinsider.com
Waste360 – Mango Materials Transforms Methane to Biopolymerwaste360.comwaste360.com
GreenBusinessBenchmark – 5 Types of Bioplastics (uses of starch-based plastics)greenbusinessbenchmark.com
Planet Pristine – Cost comparison of biodegradable materialsplanetpristine.complanetpristine.com
Our World in Data / WEF – Global plastics production and recycling datarts.comgreenbusinessbenchmark.com
OceanCare – Plastic pollution in oceans (marine animal impacts)oceancare.orgrts.com
コメント